Sintering Furnace
VARIO S430
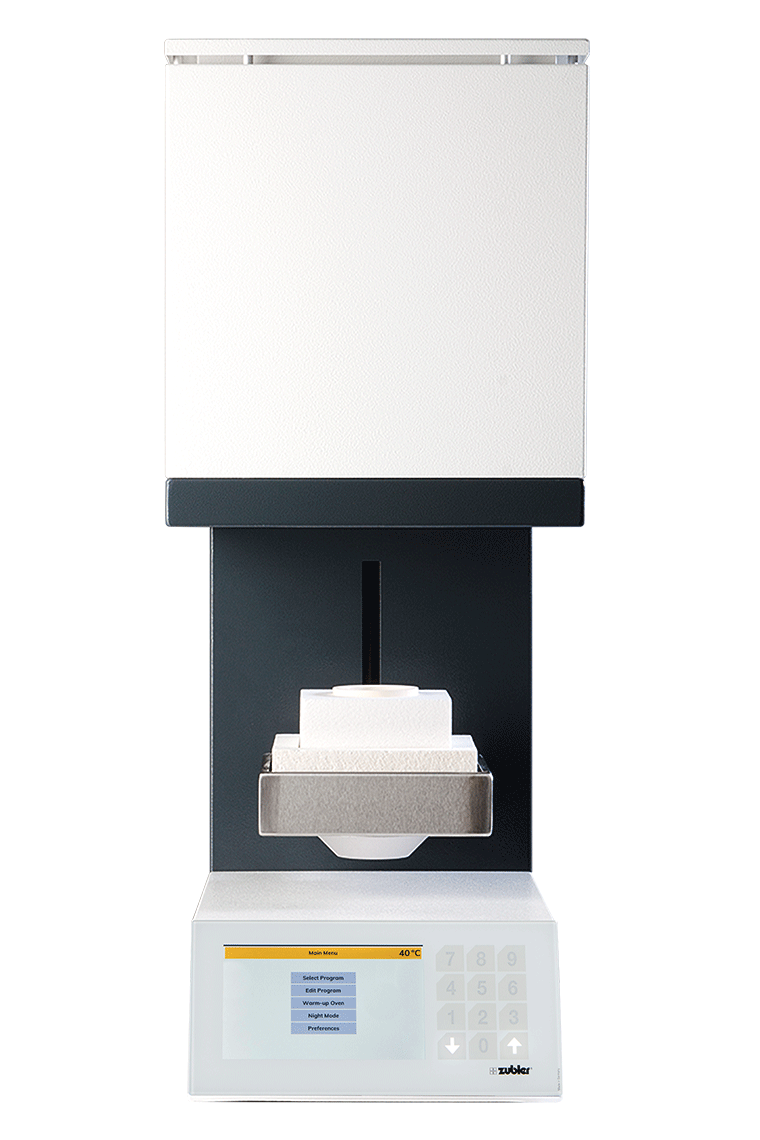
Characteristics
-
LOW CONSEQUENTIAL COSTS IN DAILY USE
-
INDIVIDUAL SINTERING PROCESS
-
TIME-TEMPERATURE-COOLING (TTC), FOR LINEAR COOLING
-
Full touch display and intuitive menu navigation
-
MOLYBDENUM DISILICIDE HEATING ELEMENTS FOR SPEED AND LONG-TERM SINTERING PROCESSES
-
2 LEVELS OF SINTERING DISHES WITH LARGE FIRING CHAMBER
-
REGENERATION PROGRAM FOR CONSTANTLY RENEWABLE HEATING ELEMENTS
-
USB Port Download Service Centre
Characteristics and Properties
The high energy efficiency of 1.12 W/cm3 and the innovative control of the heating are responsible for low consequential costs in the daily use of the furnace. In addition, they guarantee a long service life of the individual molybdenum disilicide elements (MoSi2), which can be replaced individually in case of failure
Time and energy efficiency play an important role in the modern dental laboratory. Therefore not only conventional sintering cycles, but also speed processes can be programmed in the S430 in order to be able to work with the greatest cost-effectiveness. All heating phases (maximally five) allow the free input of a heating rate from 1 °C to 100 °C/min. The sum of all holding times is 420 minutes at the most.
The proven TTC mode (time-temperature-cooling) is available to you in the VARIO S430. The special feature of this process is that the sintered objects are returned to room temperature in an actively controlled, linear cooling process in order to avoid damage.
The VP330 presents itself with a large and wellarranged full touch display. The modern and contemporary menu navigation represents more efficiency and operating comfort. Whether editing for one-time a running programme or permanently changing the programme parameters - working with the VP330 proves to be child‘s play.
The four molybdenum disilicide heating elements ensure the homogeneous distribution of heat in the firing chamber. Zirconium frameworks are manufactured to the highest quality standards, whether a conventional sintering process or the time and energy-saving speed process is used.
The newly developed Zubler sintering dish system is characterized by special material characteristics in daily use. In a similar way to a thermal protective shield, the high-purity material ensures a homogeneous distribution of the temperature inside the carrier and protects the sintering objects against discolorations.
This program protects against the „burning“ of the heating elements. A sort of protective layer is thereby formed on the surface of the heating rods and prevents deterioration in the effectiveness of the heating. The service life of the heating elements is noticeably extended.
After the successful registration of your VP330 pressing furnace in the service area of our Zubler homepage, you have access to our extensive database. To download various programmes for all dental ceramics on the market and the current software version for your pressing furnace - simply log in and download. In addition to the extended warranty, you will receive all services in the download centre and you will always be technically up-to-date.
Minimized costs of the S430 in daily operation
High-quality molybdenum disilicide heating elements reach a maximum end temperature of 1.650°C. Unlike silicon carbide heating systems, heaters of this type are far enough away from their maximum performance limit of approx. 1.800°C. Thanks to this property they attain a significantly longer service life. Each of the four heating elements can be individually replaced in case of damage – an „en bloc“ replacement is unnecessary. When calculating the energy consumption of a furnace taking into account the volume of the firing chamber, an energy density of 1.12 W/cm3 results for the S430. This very high energy efficiency means low operating costs in daily use. A type-B thermocouple is designed for a maximum temperature of 1.800°C. The processing temperature of maximally 1.650°C for zirconium oxide lies well below that – a fact which, at the end of the day, is reflected in a longer service life of the thermal sensor.
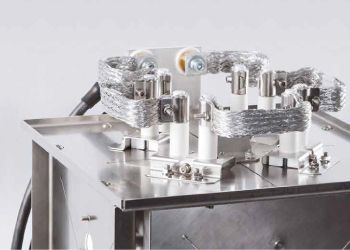
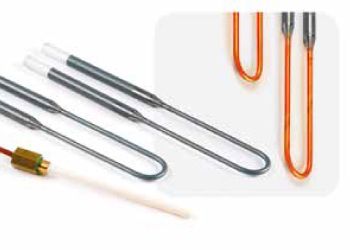